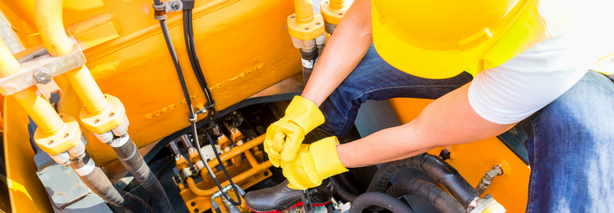
6 Steps to Implementing Maintenance Software
This article originally appeared in Grading & Excavating Contractor magazine
Switching from a fragmented mix of spreadsheets and paper-based processes to specialized software to manage equipment maintenance and repairs can have a big impact on profitability for heavy civil construction companies. The most effective companies leverage software sometimes referred to as a Computerized Maintenance Management System (CMMS) to hold maintenance costs close to the best-practice standard of five percent of total revenue. Their success, however, depends on more than the software itself. These are the top six supporting steps to overcoming resistance, ensuring an effective implementation and achieving long-term results.
Get buy-in from the top
Converting to maintenance software moves more smoothly when company owners and executives have a long-term approach, advocate for the program and dedicate the time and resources necessary. By making their vision and commitment well known, executives can prevent minor setbacks and naysayers from derailing the implementation. They also send a signal that improving maintenance results is an important, company-wide initiative. That is strong motivation for the maintenance team on the front line and for the other employees throughout the company that must also cooperate.
Confront resistance head on
Construction and maintenance pros may not be the quickest to embrace software. Resistance should be expected, especially when a system they are comfortable with and confident in is replaced with unfamiliar technology. Some employees will also feel that “Big Brother” is going to be evaluating their every move. Companies implementing a CMMS should leverage the fact that most employees also want to work with the best tools available and contribute to success. Demonstrating how software eliminates tedious tasks, allows them to perform more effectively and makes their day-to-day tasks easier will lessen the threat of the unknown. Providing adequate training and choosing software that is intuitive and easy to use are also critical to acceptance.
Don’t skimp on training
You never get a second chance to make a first impression. Training maintenance employees thoroughly at the outset is the best way to head off initial resistance to software, get them confident and ensure that they will be ambassadors for the project throughout the company. Companies make a big mistake when they fail to support an investment in the software with an incremental investment in a strong, structured training program at the outset and rely on employees just picking it up piecemeal as they go along. Accommodating varying levels of software experience is important, and ongoing training is a good idea in order to drive full utilization and continuous improvement.
Get the operations team on board
A CMMS will improve and automate preventive maintenance. That’s good the bottom line. In the field, however, taking an asset out of service can be seen as a threat to productivity, especially when it isn’t broken. The maintenance team can sell the concept that short-term shutdowns for preventive maintenance are preferable by reducing unexpected breakdowns and delivering a net increase in uptime and availability. The software should also enhance collaboration, allowing field and maintenance teams to communicate easily and in real-time regarding repair requests, work orders and equipment status.
Make parallel, supporting changes
A CMMS can do a lot more than provide a one-for-one replacement for manual and paper-based processes. Companies should be prepared to improve processes and procedures, and possibly even make staffing changes, to fully exploit the features and benefits. For example, a more proactive and automated approach to preventive maintenance might allow a company to rethink how it schedules and dispatches mechanics. Supporting the CMMS with technology like telematics capabilities for the fleet, tablets for the staff and integration with inventory, purchasing and accounting will also help to optimize the results.
Document, measure and report
Documenting the implementation plan and how the maintenance software will be used based on company-specific requirements helps to eliminate ambiguity, hold people accountable and keep the entire company informed. To get the most out of the software, a company should also develop a plan for tracking and utilizing the expanded data on equipment status, repair history and key indicators of maintenance performance such as maintenance costs as a percentage of revenue, preventive vs. corrective mechanic hours and many others.
By John Kane
John is a Product Manager for B2W Software.
Leave a Reply
Want to join the discussion?Feel free to contribute!